郭晓宁老师简介
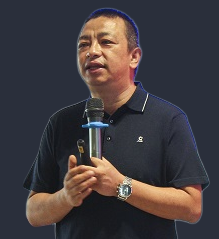
博客访问:156890
郭晓宁: 资深精益生产实战专家、IE现场效率改善顾问,国内倡导向客户承诺效果的实战型讲师/精益顾问; 国内生产管理领域专注精益<IE工业工程>降本增效培训与咨询推进者; 富士康IE学院常年外聘主力IE讲师,精益生产讲师; 美的学院特邀外部IE讲师、LP讲师; 海信学院特..
郭晓宁最新博文
- 郭晓宁讲师精益IE现场改善专题培..
- 精益改善的十大原则!..
- 精益生产改善的十三个基本要点..
- 郭晓宁讲师《精益IE现场改善专题..
- 浙江海信空调IE工业工程实战培训..
- 广东新宝电器《精益IE工业工程培..
- 郭晓宁老师深圳富士康《IE工业工..
- 江西南昌欧菲光邀请郭晓宁老师讲授..
- 郭晓宁讲师:重庆格力电器《IE工..
- 企业推行精益生产辅导项目失败的原..
郭晓宁主讲课程
企业推行精益生产失败的原因是什么?精益生产方式是目前全球企业公认的以最低成本生产出最高品质产品的管理运营方式,然而大多数企业推广和实施后并未取得预期效果,那么是什么原因导致推行精益生产失败的呢?下面华谋精益生产咨询专家就来为大家解析如下: 最近有个流行词叫“企业家精神”,需要站在企业的角度看问题。然而,许多企业家或者管理层,却无法站在员工的角度看问题,也许是忙得顾不上,也许是觉得自己不专业,又或是觉得精益生产就是生产员工的事情,自己不关心,不参与精益生产活动,又怎么让员工自己把它做好?管理层带头做榜样,下面的员工才会更有积极性的参加,实现领导到头,全员参与的格局。 三、缺乏开展精益生产的动力 管理层要求精益生产,是因为有成本压力,有财务目标。但是员工呢?每个人都有惰性思维,更喜欢做自己最熟悉的事情,这样效率更高,错误更少,可以很舒服的拿工资。然而精益的本质就是改变,改变是很可怕的,不会有很多人自发的去改变。管理层要解决精益生产的动力,精神鼓励也好,物质刺激也罢,只有让全员参与的精益生产,改善活动才能真正的行之有效。
四、精益生产需要持续改进 很多人把精益当成了培训课程,认为搞一次宣讲,讲一下方法,做一个样板就算完成了改善,殊不知这只是精益的开始。有专家说过一个养成一个新的习惯需要九十天,做出任何的改善都无法一蹴而就。尤其是一些改变并不是自发的情况下,长期坚持尤为重要。 五、精益生产看不到结果 做改善是否成功,需要用最终的收益来判断,只要能抓住老鼠都是好猫。这里提醒的结果导向,是告诉大家不要为了精益而精益。做精益没有套路和教条,更不能生搬硬套他人的成果,这是很多运动式的精益失败的原因。要理解我们要的精益生产,是要改善自己的现状,即使我们照着丰田的精益模式做改善,也不可能能成为下一个丰田。 |